CHEMICAL AND PHARMACEUTICAL CENTRIFUGES
The Western States Machine Company has been designing and manufacturing high-performance vertical filtering and decanting centrifuges for solid-liquid separation for the chemical, fine chemical, food, and pharmaceutical industries since 1950. From the very beginning, Western States has focused entirely on the innovative design of vertical centrifuges to offer our customers cost-effective separation solutions.
Centrifuges For the Chemical Industry
In the chemical industry, centrifuges are utilized for tasks such as clarifying liquids, separating immiscible liquids, dewatering solids, and purifying products. Their versatility allows for the processing of diverse substances, including chemicals, solvents, polymers, and intermediates, among others.
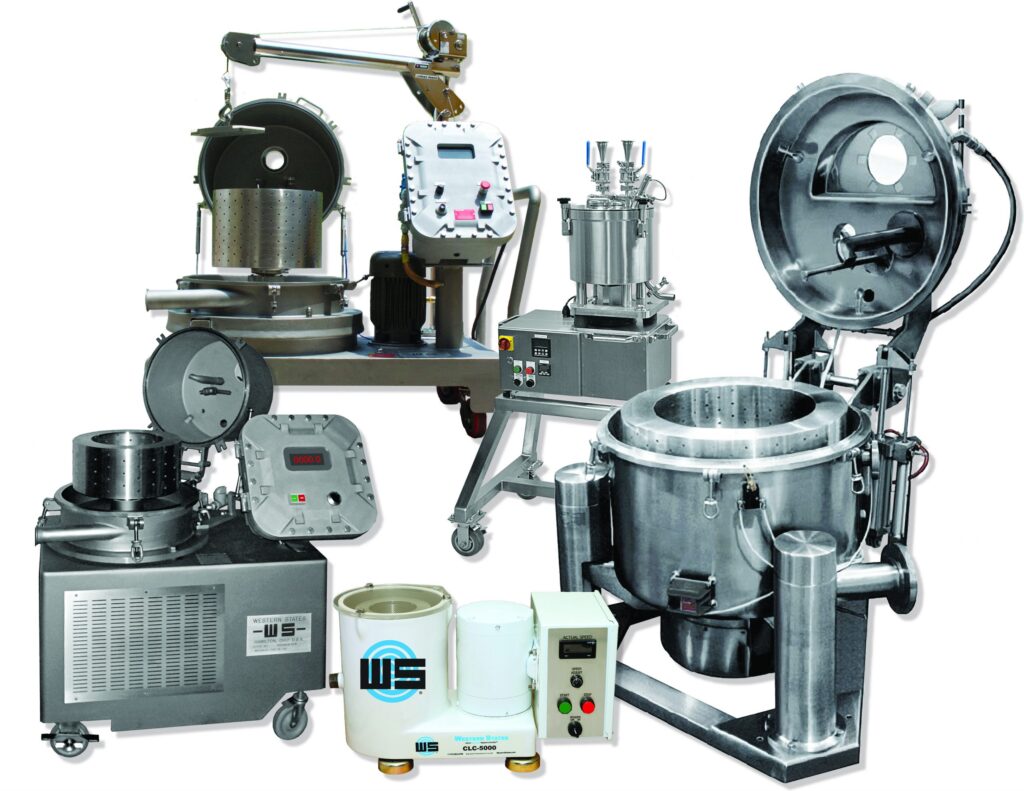
Chemical centrifuges come in various types and configurations, such as mini centrifuges, benchtop centrifuges, ultracentrifuges, and full-scale laboratory centrifuges, to accommodate different process requirements and scales of operations. From small-scale laboratory centrifuges to large industrial centrifugal separators, these machines are designed to handle separation of solutions with different volumes, viscosities, and particle sizes with precision and reliability.The efficiency and effectiveness of chemical centrifuges directly impact the quality, yield, and cost-effectiveness of chemical processes. By facilitating rapid separation and purification, centrifuges contribute to enhanced product quality, increased productivity, and improved resource utilization in chemical manufacturing operations.
Since 1950, Western States has custom designed and manufactured over 1,000 vertical filtering and decanting centrifuges. Many well-known producers from the chemical, pharmaceutical and food industries have come to trust the Western States brand of vertical centrifuge to provide trouble-free solid-liquid separation.
Why Choose a Specialized Chem/Pharma Centrifuge?
Chemical and pharmaceutical centrifuges are vital tools in various industries, facilitating the separation of solid and liquid components in chemical processes, as well as the production of consumables for the pharmaceutical market. These centrifuges employ high-speed rotation to achieve efficient separation, making them indispensable in diverse applications within the chemical sector.
Advancements in centrifuge technology, such as automation, control systems, and advanced materials, continue to enhance their performance, reliability, and operational flexibility in the chemical industry. As a result, centrifuges remain indispensable assets for chemical manufacturers seeking to optimize their production processes and maintain competitive advantages in the market.
Importance of Chemical and Pharmaceutical Centrifuges
Chemical and pharmaceutical centrifuges play a crucial role in ensuring product quality, process efficiency, and regulatory compliance. They enable precise separation of substances, purification of products, and removal of impurities, thereby enhancing the overall manufacturing process.
Factors Influencing Chem/Pharma Centrifuge Performance
In the intricate world of chemical and pharmaceutical manufacturing, the efficiency and reliability of centrifuges stand as linchpins. From speed and size to material compatibility and regulatory compliance, each facet plays a crucial role in ensuring optimal performance and maintaining product integrity throughout the separation process.
Speed and Acceleration
The rotational speed and centrifugal force applied significantly impact the performance of industrial centrifuges. Optimal speed settings are crucial for achieving efficient separation without compromising product integrity.
Size and Capacity
The size and capacity of a centrifuge dictate its throughput and suitability for different batch sizes. Choosing the right size ensures optimal performance and resource utilization in chemical and pharmaceutical processes.
Material Compatibility
Centrifuge materials must be compatible with the substances being processed to prevent contamination and ensure product purity. Compatibility considerations include chemical resistance, corrosion resistance, and adherence to regulatory standards.
Contamination Control
Effective contamination control mechanisms are essential for maintaining product purity and preventing cross-contamination in chem/pharma centrifuge applications. These mechanisms may include sealing systems, sterilization procedures, effective wastewater management, and clean-in-place (CIP) protocols.
Preventative Maintenance Applied
Regular preventative maintenance is critical for sustaining centrifuge performance and prolonging equipment lifespan. This can help prevent future downtime, as well as address any potential issues with centrifuge rotors, centrifuge tubes, o-rings, test tubes, or any other components within a centrifuge before breakdown occurs.
Regulatory Compliance
Compliance with regulatory standards, such as Good Manufacturing Practice (GMP) guidelines and industry-specific regulations, is paramount in chemical and pharmaceutical manufacturing.
Benefits of Using Western States Chemical and Pharmaceutical Centrifuges
Western States Chemical and Pharmaceutical Centrifuges are vertical filtering and decanting centrifugals that stand out with their innovative design, customizable solutions, stringent quality assurance, proven track record, and unmatched versatility, meeting diverse industry needs with precision and efficiency.
Innovative Design
Western States focuses on pioneering vertical centrifuge designs tailored to meet specific chemical and pharmaceutical industry needs.
Customization
Our engineers have flexibility to adapt and custom design state-of-the-art centrifuges and automation systems to meet each customer’s specific requirements with finite element analysis and advanced 3-D modeling.
Quality Assurance
Centrifuges adhere to the latest Good Manufacturing Practice (GMP) standards, ensuring reliability and compliance. Every Western States Centrifuge is manufactured in accordance with the latest GMP standards, requirements, or directives and is backed by superior support and service.
Proven Track Record
With over 1,000 custom-designed centrifuges manufactured since 1950, Western States has earned the trust of leading producers in the chemical, pharmaceutical, and food industries.
Versatility
Western States centrifuges cater to a wide range of applications, from laboratory development to full-scale production, providing solutions for separation, filtration, clarification, and drying needs.
Chemical and Pharmaceutical Machines at Western States
Since 1950, Western States has custom-designed and manufactured over 1,000 vertical filtering and decanting centrifuges from our USA-based facilities. Many well-known producers from the chemical, pharmaceutical, and food industries have come to trust the Western States brand of vertical centrifuge to provide trouble-free solid-liquid separation.
Whether your product is in the laboratory development stage, pilot plant testing stage, small-scale production, or full-scale processing; Western States can provide high-quality equipment for your separation, clarifying, or drying needs.
- Solid–Liquid Separation
- Liquid–Liquid Separation
- Solid–Liquid-Liquid Separation
- Instantaneous Drying
- Particle Reduction
Choosing the Right Chemical and Pharmaceutical Centrifuge
Selecting the appropriate centrifuge for chemical and pharmaceutical applications requires careful consideration of factors such as speed, capacity, material compatibility, and regulatory compliance. Western States offers a comprehensive range of centrifuges designed to meet diverse industry requirements.
More Information on our Chem/Pharma Products
CENTRIFUGE APPLICATION
Click below to download and complete our Centrifuge Application Form. Email the completed form to ws.sales@westernstates.com or FAX the form to +1 513.863.3846. We will contact you as soon as we receive your form.