Q-SERIES CENTRIFUGES
QUADRAMATIC CENTRIFUGES
The Quadramatic™ centrifuge machine is a vertical, bottom-discharging or top-unloading filtration centrifuge developed to generate up to 2,000 gravities of separation force. When operated as a filtering centrifuge, the Quadramatic™ can remove most, if not all, of the unbound moisture without the need for thermal processing to deliver a cost-effective and dependable method of separating solids and liquids for medium to full-scale production.
The Quadramatic™ filtering centrifuge features several design components developed to produce highly dependable performance during continuous and fully automatic operation available in capacities from 1.9 ft³ to 33 ft³ in a wide range of chemical applications.
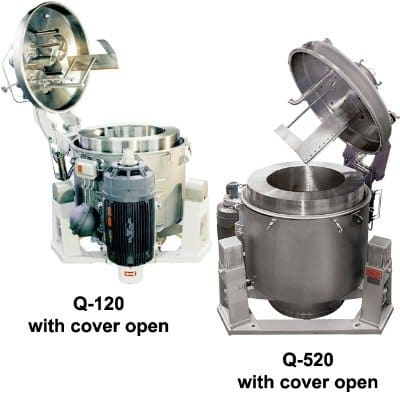
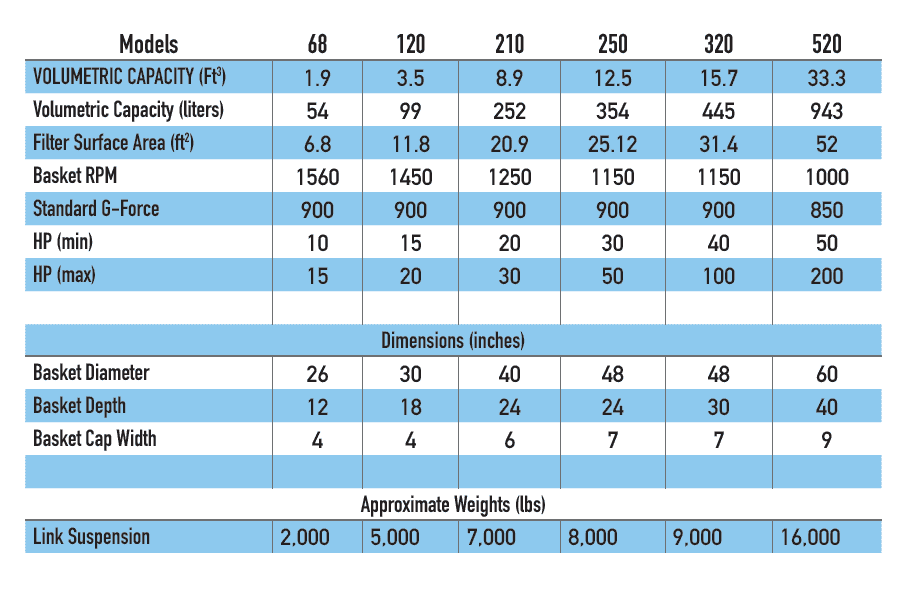
DESIGN FEATURES
BASKET
The Quadramatic™ utilizes state-of-the-art separation technology, including a highly perforated centrifuge filter basket to provide efficient purging of the liquid to provide maximum loading and to avoid the creation of a water wall to minimize excessive gyration. All Western States centrifuge baskets are designed to be the safest in the centrifugal filtration industry with a 2.0 Safety Factor. The internal and external surfaces of the basket’s side sheet and bowl wall are fully machined and parallel. The finished basket seam is fully X-ray inspected and dynamically balanced for optimum performance at 900 plus “G” force. A wide range of filter media, including backing layers and plow plates can be combined to create a special basket centrifuge filter system for your product.
LOAD SENSOR
A special design feature of the Quadramatic™ centrifuge is our patented Ultrasonic Load Control System used to accurately monitor and control the feed rate and cake depth for ultimate separation performance. The Load Sensor employs no moving parts and never touches the cake for non-invasive and reliable cake detection. The Load Sensor also provides the added benefit of assuring maximum discharge of the high-value solids to minimize any product loss.
DISCHARGER
The Quadramatic™ centrifuge features the Monocut™ Discharger which has a full-length plow blade with a replaceable cutting tip. The Monocut™ Discharger removes the sedimentation in a single inward (horizontal) motion. The single in-and-out movement of the discharger eliminates the need for vertical seals which can be sources of contamination. A Heel Removal System can be added to the discharge which directs air to assist in the removal of the residual product cake for maximum solids recovery during the separation process.
EASE OF MAINTENANCE
The Quadramatic’s™ vertical tapered basket spindle and heavy-duty ball and roller bearings are designed for high strength, stability, and long life and are easily maintained. The bearings can be simply lubricated by grease fittings positioned on the outside of the centrifuge enclosure. The sealed area between the top of the bearing housing and the bottom of the basket can be purged with clean air or inert gas to provide an extended bearing life of the industrial centrifuge.
OTHER AVAILABLE DESIGN FEATURES
The Quadramatic™ is available with various styles of access covers for internal component inspection including a full opening hydraulically actuated, hinged domed cover for optimal inspection and user experience. The covers are of fume-tight construction and can be designed as a pressure or vacuum vessel. All of our access covers allow operation with a wide range of volatile, explosive, or toxic materials. Oxygen sensors confirm inert gas blanketing by assuring the residual oxygen is maintained at a safe level. Additional cover accessories are available including: sight glass, fume vent, various feed and wash pipes, and the Quadramatic™ CIP Option.
CLICK TO DOWNLOAD THE WESTERN STATES QUADRAMATIC™ TECHNICAL SPECIFICATIONS AND PRINCIPLES OF OPERATIONS
STANDARD AVAILABLE OPTIONS
(QUADRA-CLEAN AND QUADRAMATIC)
MATERIALS OF CONSTRUCTION
The construction material and filter medium of each Quadra-Clean™ is chosen to meet the customer’s particular requirements.
Baskets and all other components in contact with the product can be provided in any workable metal including the full range of stainless steels, nickel, Inconel, Monel, Hastelloy, titanium, duplex stainless, and other exotic metal alloys. Also available are rubber and elastomer linings, plus all the latest protective coatings including HALAR and TEFLON.
Surface finishes range from satin bead blast to mechanical polishing to electrochemical polishing to provide a mirror-like finish for the most stringent of sanitary applications. All the internal and external welds will meet or exceed applicable industry standards
CIP SYSTEM
The CIP System (Clean in Place) feature is used to clean the centrifuge process zone between batches of a single product or between products. Carefully placed CIP nozzles spray all surfaces of the centrifugal device with even coverage. As the basket revolves, the nozzles saturate the upper surfaces and the lower section is thoroughly flooded to clean all surfaces of the filter unit. The CIP option can be included with any Western States vertical centrifuge to eliminate the risks of cross-contamination. The CIP system can be validated via a Riboflavin Test during the FAT (Factory Acceptance Test) to demonstrate all the process surfaces are contacted with the cleaning solvent.
AUTOMATION & CONTROLS
Western States is a leader in the use of programmable control systems and variable frequency drives for centrifuge automation. We offer a wide range of systems with state-of-the-art components to meet most customer requirements to provide maximum processing flexibility and ultrafiltration. Operating modes range from fully automatic via a PLC to manual control. A full range of NEMA enclosures and types are available including explosion proof designs rated for Class I, Division I, and Groups C & D Service.